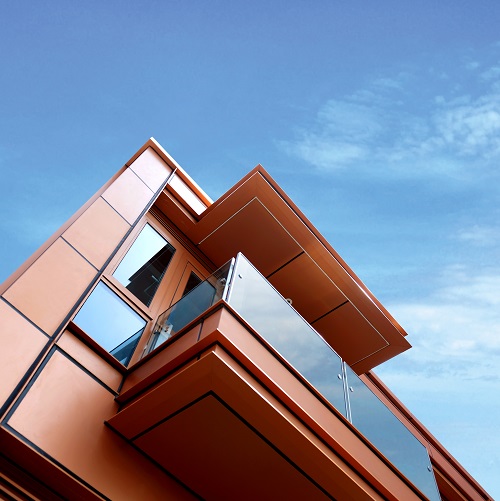
Modular Integrated Construction (MiC) is an innovative construction method. By adopting the concept of “factory assembly followed by on-site installation”, MiC helps to ease some of the current challenges faced by the local construction industry. In this method, free-standing integrated modules (completed with finishes, fixtures and fittings) are manufactured and assembled in a factory. By transferring on-site construction processes to a controlled factory environment, buildings can be substantially completed off-site. The adverse impacts of weather conditions, scarce labour resources and site constraints can all be substantially reduced. MiC provides a great degree of production quality control, and can improve construction productivity, safety and sustainability.
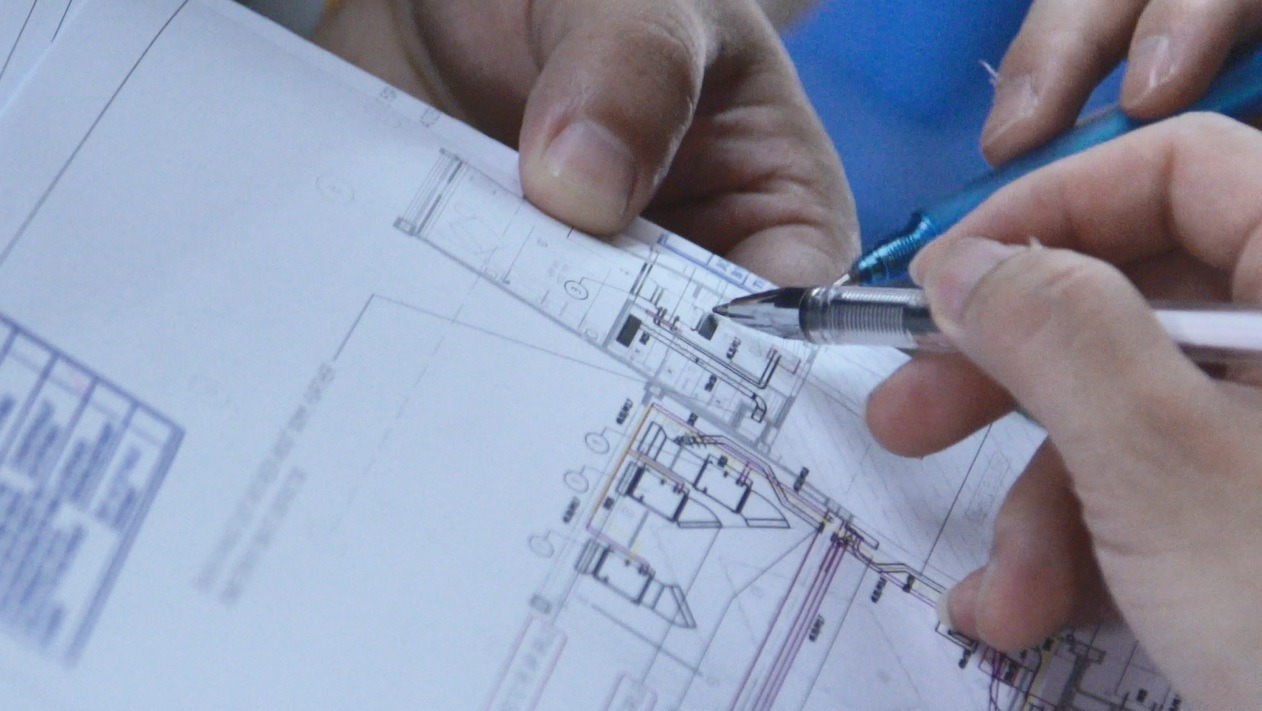
General Process of MiC
1. Project Design
- Early engagement of module supplier and local contractor is needed
- Design needs to be completed at an early stage
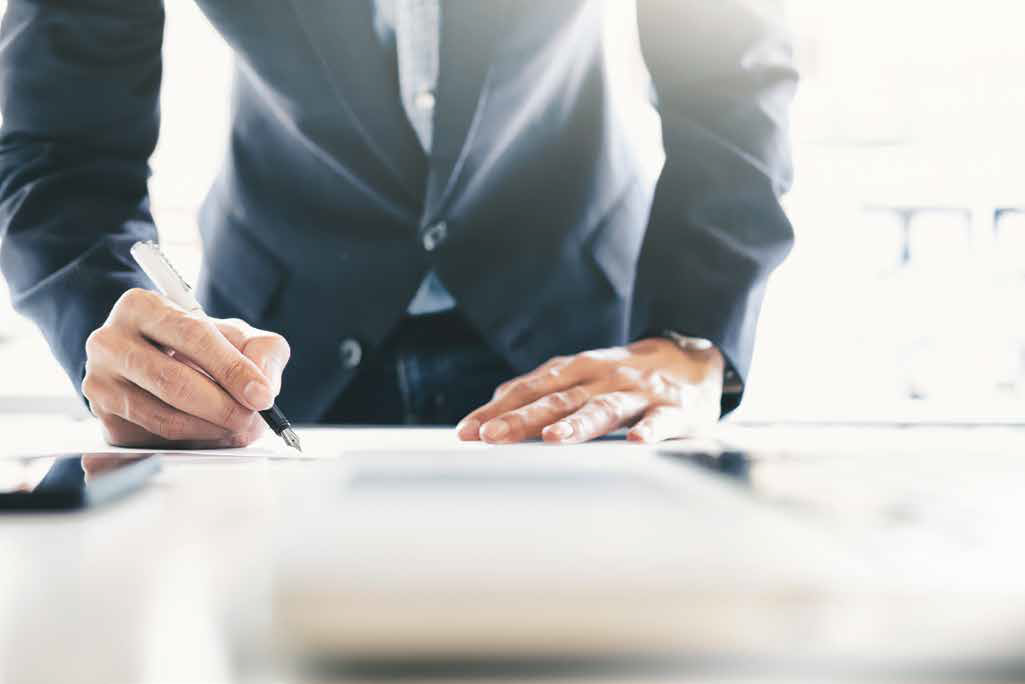
2. Seeking Statutory Approvals
- The design needs to comply with the Buildings Ordinance and/or other relevant requirements (e.g. PNAP ADV-36 ) and procedures
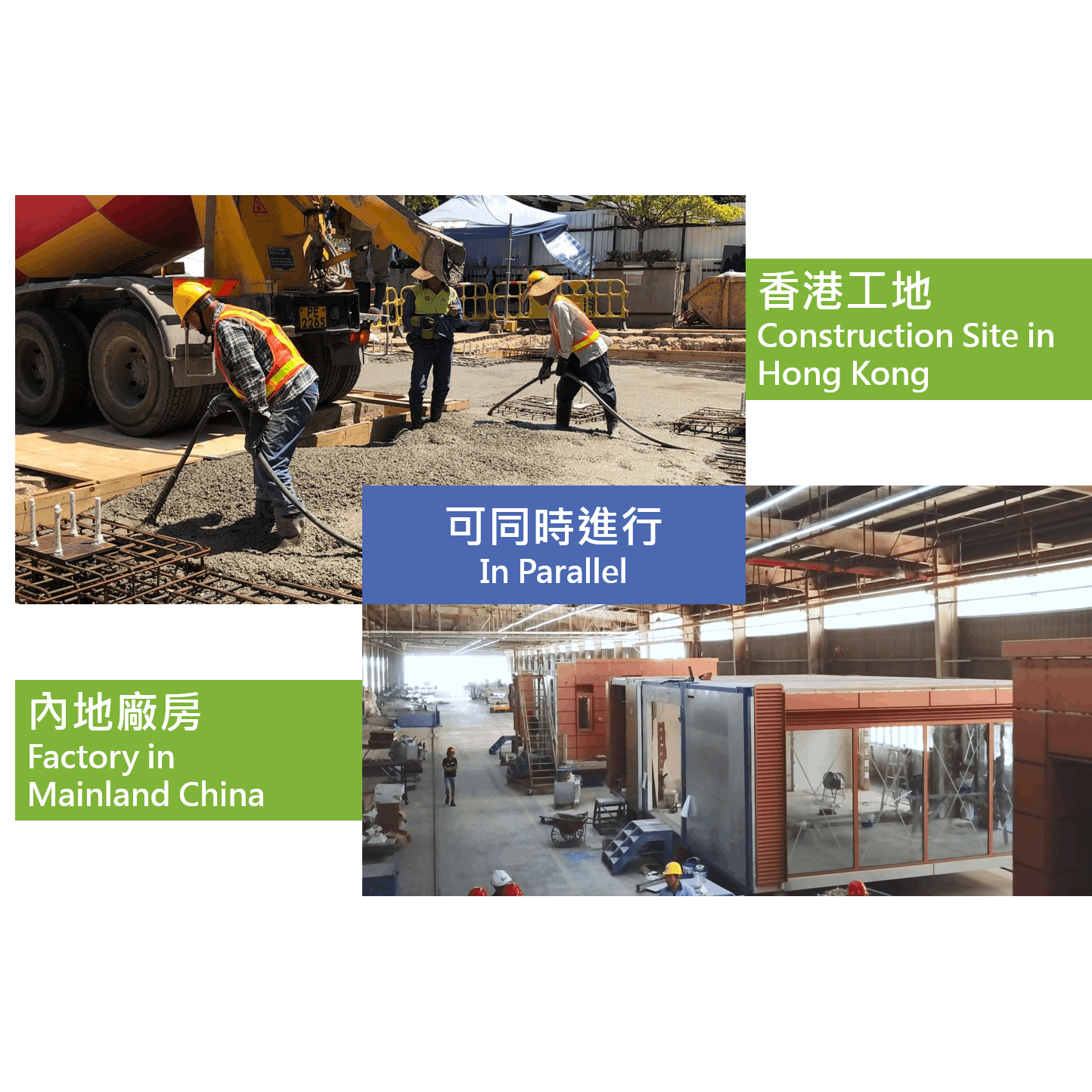
3. Production of Modules
- Mock-ups and prototypes of each type of module are fabricated, checked and tested before mass production
- Trial assembly/stacking of modules in the factory should be carried out
- On-site construction activities, such as piling/foundation works, external underground utility works, etc., can be carried out concurrently
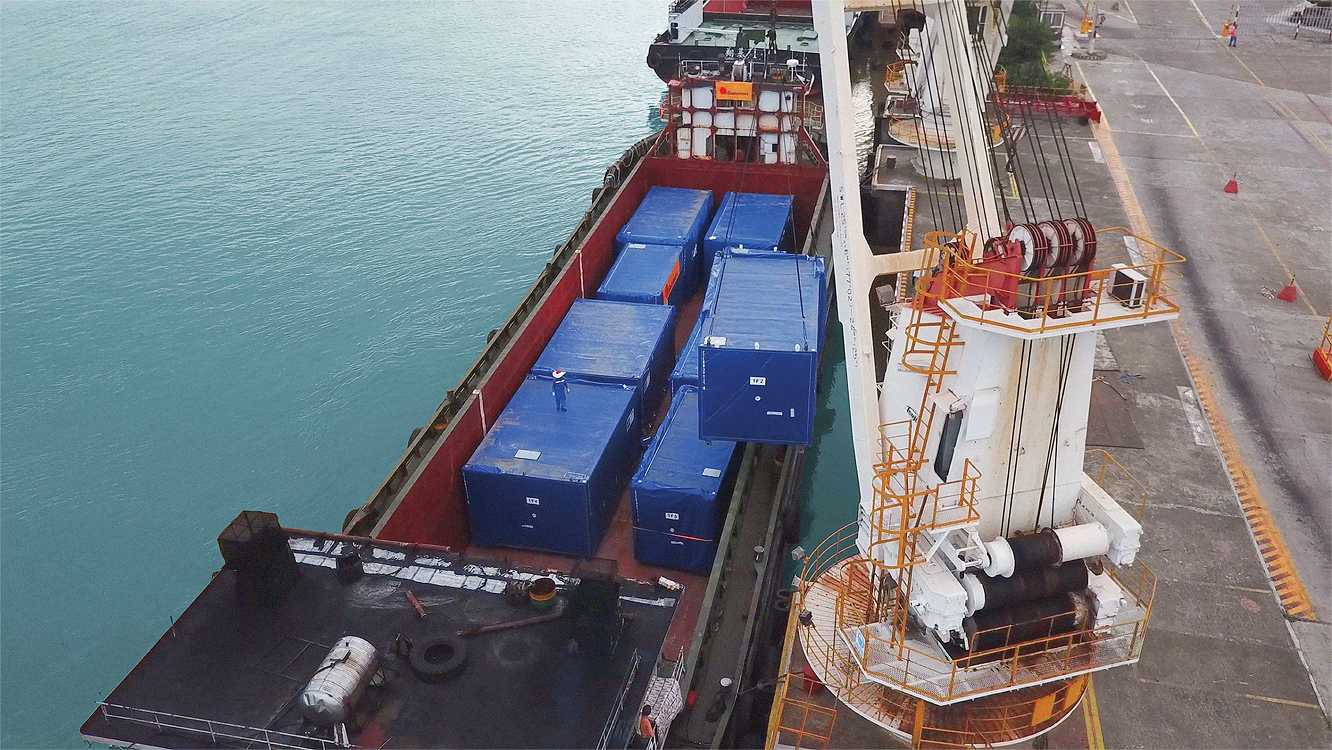
4. Transportation of Modules to Site
- Special traffic arrangement needs to be made for transportation of modular units with width larger than 2.5 meters
- Temporary storage location may need to be arranged, subject to the delivery and construction programme
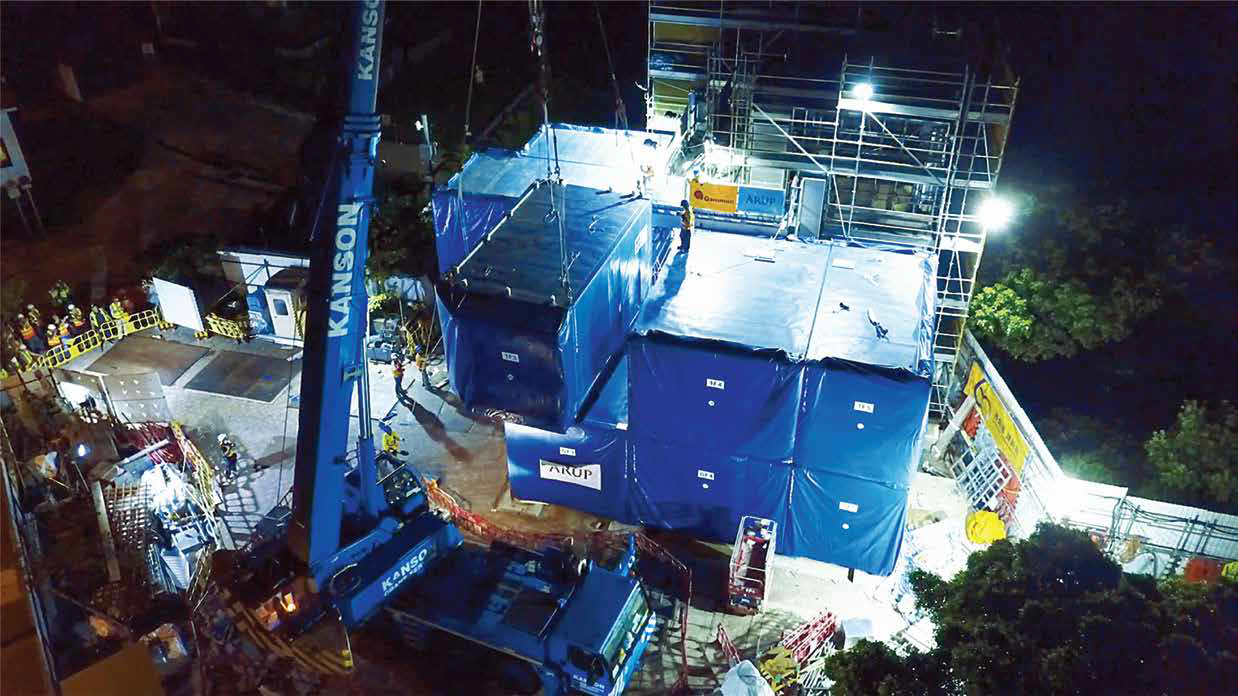
5. On-site Installation
- Upon stacking of modules, temporary waterproofing is required to be carried out before completion of permanent waterproofing
- Connection of module to module/module to core parts (Structural and Mechanical, Electrical & Plumping Systems) needs to be made
Design for Manufacture and Assembly
Design for Manufacture and Assembly (DfMA) is a design approach that emphases the ease of manufacture and efficiency of assembly of construction components. It enables off-site manufacturing for on-site assembly, which can reduce on-site construction processes.
Prefabrication components and MiC, both of which replace conventional site operations with off-site prefabrication, are examples of DfMA.
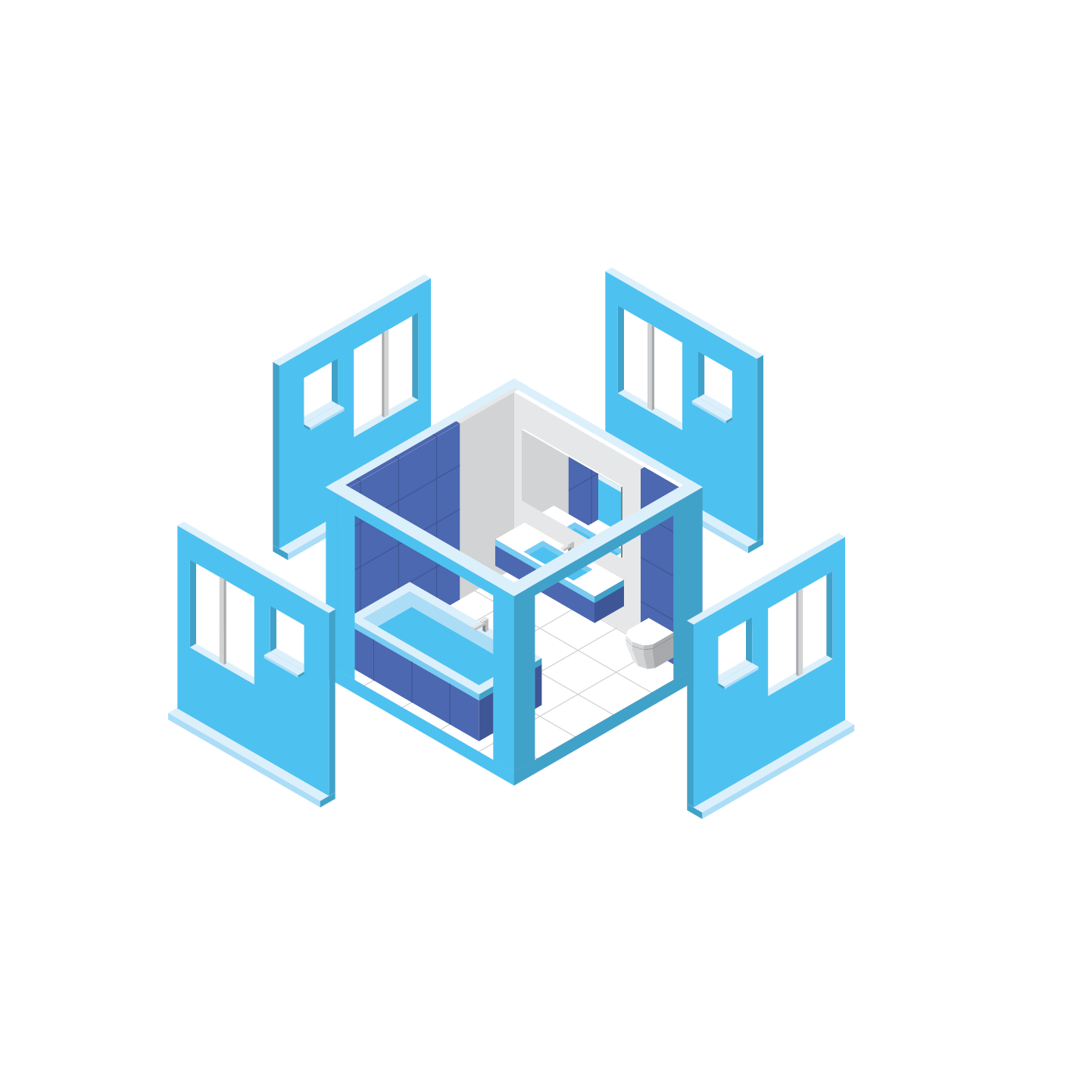
Differences between Prefabrication Components & MiC
Prefabrication Components
- Prefabricated components only comprise small parts of a building
- Structural parts other than prefabricated components still need to be built using conventional construction methods
- Substantial amount of formwork, steel fixing, and concreting works are involved
- Interior decoration and laying of pipes, etc., could only be carried out thereafter
Common Prefabrication Components in Building Works
- Prefabricated Facades
- Prefabricated Slabs
- Prefabricated Walls
- Prefabricated Staircases
- Semi-prefabricated Slabs
- Prefabricated Bathrooms
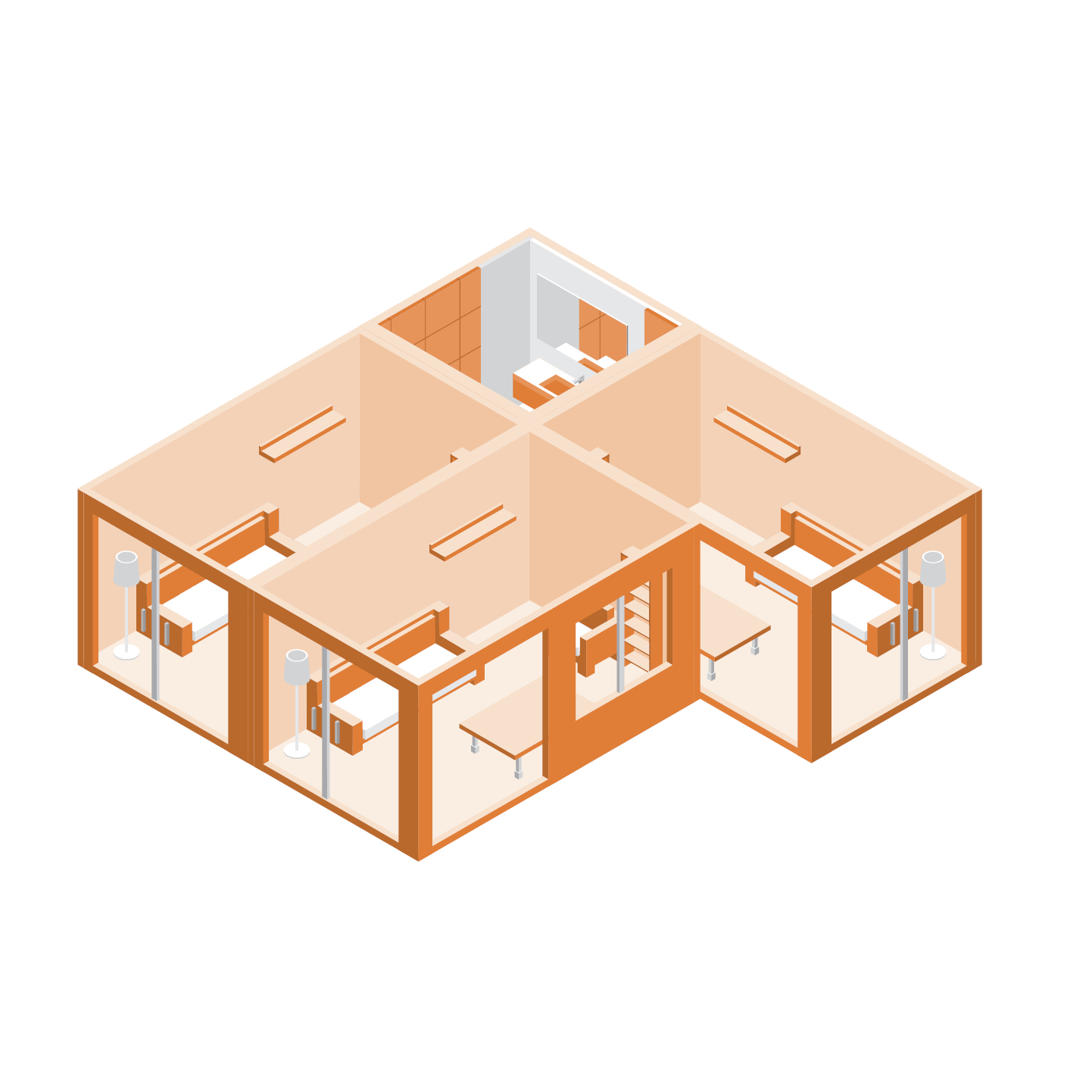
Modular Integrated Construction
MiC is an innovative construction method. By using MiC, the building is substantially completed off-site. This can reduce on-site construction processes and enhance site safety, hence achieving higher productivity.
- Free-standing integrated modules (completed with finishes, fixtures and fittings) manufactured in a factory
- Modules transported to construction site
- Modules installed to form a building
Various Types of MiC
- Reinforced concrete modules
- Steel frame modules
- Hybrid modules
The Construction Innovation and Technology Fund (CITF), with an approved allocation of HK$1 billion, was established by the Development Bureau of the Government of Hong Kong Special Administrative Region (DEVB) in October 2018. The Construction Industry Council (CIC) is commissioned by DEVB to be the implementation partner.
The CITF covers two aspects, namely technology adoption and manpower development. The former aims to encourage the industry to use new but proven technologies developed within or outside Hong Kong. The latter aims to build an innovative culture and foster the mind-set to espouse new technologies for the sustainable development and continuous improvement of the construction industry.
MiC is one of the categories under technology adoption, providing incentives for consultants and contractors to widely adopt MiC in the construction projects of Hong Kong.
In mid-July of 2022, the Steering Committee of the CITF approved the MiC Vetting Sub-committee's proposal to include MiMEP into the funding scope to better support the Electrical & Mechanical (E&M) industry to adopt innovative technologies. For more details, please click here.
Adopting MiC to Build Light Public Housing (LPH) to Expedite Housing Supply


